Most successful companies share one common priority: their employees’ safety. Upholding that priority often comes with the need for fall protection. Yet with regulatory requirements to meet and an often steep price tag, fall protection can seem like a daunting undertaking. However, with the right knowledge, implementing a fall protection system can easily fit into any company’s workflow and budget.
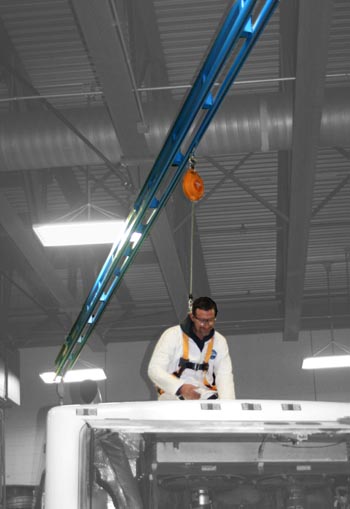
Legally, the Occupational Safety and Health Administration (OSHA) mandates that fall protection be provided at: 4ʹ in general industry; 5ʹ in shipyards; 6ʹ in the construction industry; 8ʹ in longshoring operations; and any height when working over dangerous equipment or machinery.
In some instances, companies can “engineer” the hazard out of the workplace and eliminate the fall hazard altogether by simply changing a work process. Minor adjustments such as moving work to the ground level or relocating equipment are simple ways to eliminate a fall hazard. When possible, this is one of the more budget-friendly ways to ensure worker safety as it usually does not involve purchasing much extra equipment. However, in some cases, changing the workflow or moving equipment can be more costly than the price of other fall protection options.
When the risk cannot be eliminated, companies should look to prevent the risk with equipment such as handrails, safety gates, guardrails and rooftop railings. This type of equipment is generally less expensive than a custom-engineered system. However, if work processes change, such equipment may no longer protect against falls, necessitating the need for more equipment or a more in-depth fall protection system. Because these systems cannot adapt as the company’s processes change, such methods are often not the most long-lasting of investments.
For companies who have not found success with eliminating hazards or preventing falls, restraint systems can be a worthwhile budget spend. These systems can either keep workers from reaching an area where the fall hazard exists, or enable workers to perform their duties from the height required while attached to the system. Though relatively inflexible once installed, when practical, restraint systems can be a reliable and long-lasting investment.
In many instances, none of the above practices fit a company’s needs or workflow. For these cases, fall arrest systems are the perfect option.
Fall arrest systems stop the fall in a controlled manner with either wire rope or rigid rail. Wire rope systems require additional fall clearance due to the initial sag of the wire and the stretch of the line during a fall adds to this distance. After a fall however, a wire rope system must be replaced and recertified by a qualified engineer—adding to the overall cost of the system.
Rigid-rail fall arrest systems stop the fall in a shorter distance by eliminating any sag. Injuries occurring after the fall, such as swinging into objects, are also minimized with rigid rail, as the system doesn’t sag thereby minimizing the total fall distance. In the event of one worker’s fall, the rigid-rail system does not bend or deflect like a wire rope system, thus eliminating the risk to another worker and allowing other workers on the system to continue moving freely and safely allowing them to assist in the rescue of the fallen worker. Often thought of as more expensive than other fall protection methods, rigid-rail systems allow for longer distances between supports without sag, which reduces both material and installation costs making them no more expensive to install and less expensive over the life of the system.
It can be overwhelming to select a fall protection option when balancing so many factors—productivity, profitability, safety and budget. Yet, fall protection comes in many forms and when such systems are necessary it is imperative to prioritize safety over all other objectives.